An automatic tool changer for the lathe
Here's a random collection of pics I appreciate that there's almost no detail here.E-Mail me if you'd like to know more.
Y'know I was pretty happy with the cnc conversion of the lathe . Sure I needed to tweak a few things, but it was pretty functional and had produced some good results.
Then I used Daves CNC'd Herbert turret lathe (not my friend Dave, but another mate of the same name)...
As an aside, there is no doubt that a turret lathe is THE machine of choice for a CNC conversion. They are physically quite small, massively rigid, have collet chucks and can be had for next to nothing.
But I digress. One of the features of "Daves" lathe is a, very clever, automatic tool changer.
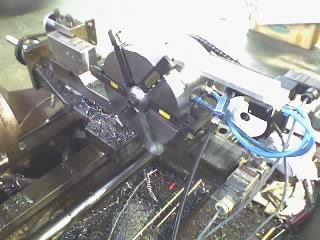
Before using this, I was content with my quick change toolpost.
But nothing beats being able to call upon any tool in a program, have the machine swing it into place, automatically compensate for it's length and width, then keep cutting!
Dave based his design on Ron Kliewers efforts
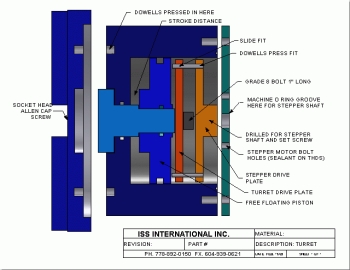
Now my machine is a fair bit smaller and lighter so I racked my brains for a while trying to come up with a simpler way to achieve the same result.
I almost settled on a small worm drive gearbox, turning a turret. EMCO have a design that works this way.
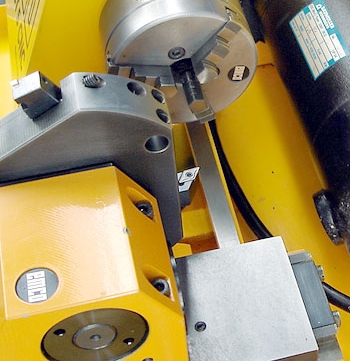
But it's just not as rigid as this set up.
With Rons design, a 4" diameter ram applies about 500lb of clamping force, locking the turret down onto 8 hardened pins located near the outside edge of the changers body.
When you are cutting, these pins support the tool very close to the tip and ensure a rigid setup.
If I had used a gearbox, I may have ended up supporting the tool from the turret axle. This would certainly have caused problems. The EMCO design used a pawl ran the changer motor backwards after the desired tool position was reached, holding the turret against said pawl. Not a bad design, but you can only run the changer in one direction. I worked on some ideas to replace the pawl with a spring loaded plunger, but concluded that this was harder (ie required more precision) than Ron's design.
Eventually I swallowed some pride and reasoned that there was not much point in fundamentally changing a demonstrably good bit of gear!
I machined the body of the changer from the end of a high pressure, aluminium, tank. This went fairly well and I soon had the seals in place and an axle made up. |
![]() |
![]() |
I used a snap ring to hold the large PVC piston in place as there is no requirement
to clamp down on the piston. In fact, the thing wouldn't work if you did. When the piston moves the turret plate off the pins, the axel turns inside the piston which doesn't rotate at all. This drastically reduces the torque required to turn the axel. |
Because my changer body has thinner walls than Ron's or Dave's I decided to thread the rear closure on. I scored a lump of aluminium from a scrap dealer and
turned up the back from solid. I also made a stub axel that slides over the main axel. The idea is to cross pin this and have the pin engage a slot in the
main axel. That way the motor can be rigidly fixed to the back plate and turn the main axel when it slides forward. |
![]() |
For the turret plate, I just bought a 50mm slice of K1045, same as Dave did | ![]() |
![]() ![]() And spent most of a morning turning much of it into swarf! |
The slots and hole for the tools get cut by putting a milling cutter in the lathe chuck after the toolchanger is mounted on the lathe
Although it is my intention to use an arrangement of tapered blocks and slots to clamp the tools in place like this:
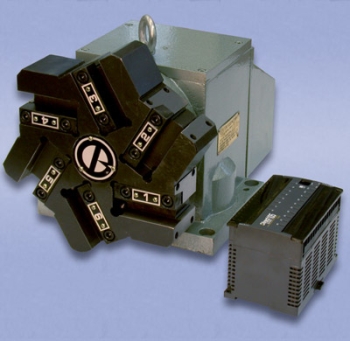
So some rework in the mill will be needed.
So this mechanism needs to somehow get mounted to the cross slide of the lathe. A 6" cylinder isn't going to fit into a toolholder, so something has to be done.
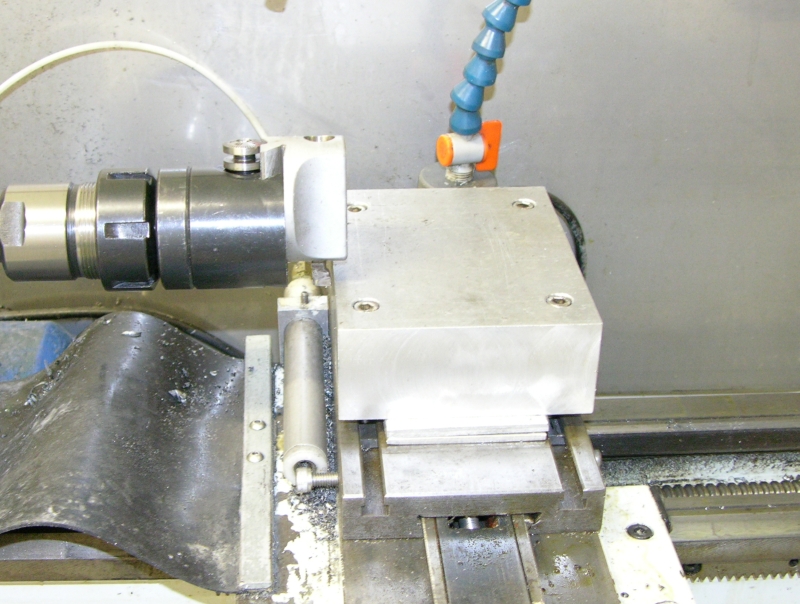